Die Casting
KEFA’s die casting or precision casting plants are industrial facilities that specialize in the production of metal components through the process of die casting or precision casting. These processes allow for the mass production of complex and highly accurate parts with excellent surface finish.
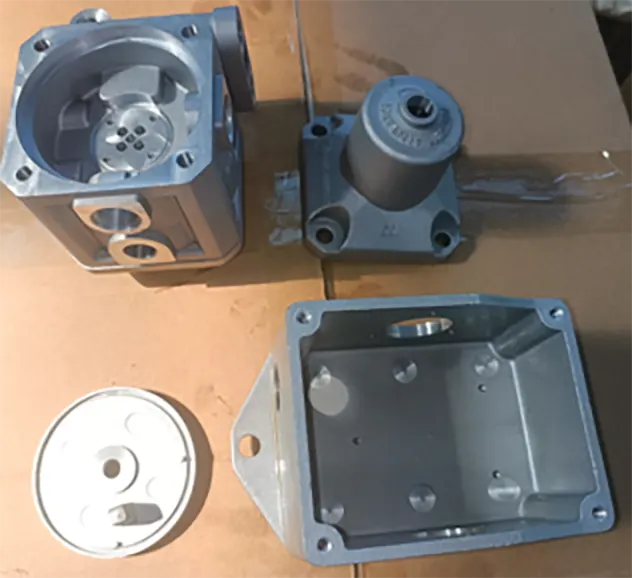
The following process steps are a summary of the die casting and precision casting processes in a plant
The first step involves designing and manufacturing the dies or molds used in the casting process. Dies are typically made of steel and consist of two halves that create the mold cavity when brought together. The molds are precision machined to ensure accurate part production.
The metal, usually non-ferrous alloys such as aluminum, zinc, or magnesium, is melted in a furnace to reach the desired temperature for casting. The melting process may involve the use of electric resistance or induction furnaces.
- Die Preparation:
The dies are preheated to improve the casting process and extend the life of the dies. They are then lubricated to facilitate the release of the cast part. - Injection:
The molten metal is injected at high pressure into the die cavity using a hydraulic or mechanical press. The metal fills the cavity, taking the shape of the mold. - Cooling and Solidification:
The injected metal rapidly cools and solidifies within the die. Cooling time depends on the part's size and thickness. - Ejection:
Once the metal has solidified, the die opens, and the casting is ejected using ejector pins or other mechanisms. The dies then close again to repeat the process.
The castings undergo various finishing operations such as removal of excess material, grinding, machining, deburring, and surface treatments to achieve the desired final shape, dimensions, and surface finish.
The finished castings are thoroughly inspected and subjected to quality control measures to ensure they meet the required specifications and standards. Non-destructive testing, dimensional checks, and material analysis may be performed.
Depending on the specific requirements of the castings and the material used, heat treatment processes such as annealing, quenching, and tempering may be applied to enhance their mechanical properties.
The finished castings are stored in designated areas and prepared for shipping to customers. Packaging, documentation, and logistics management are important aspects of this stage.
complex and highly specialized facilities
A die casting or precision casting plant requires skilled technicians, engineers, and quality control personnel to operate the machinery, monitor the casting process, and ensure the production of high-quality components. Advanced equipment such as die casting machines, furnaces, injection molding machines, and precision machining tools are utilized to achieve efficient and precise casting production.
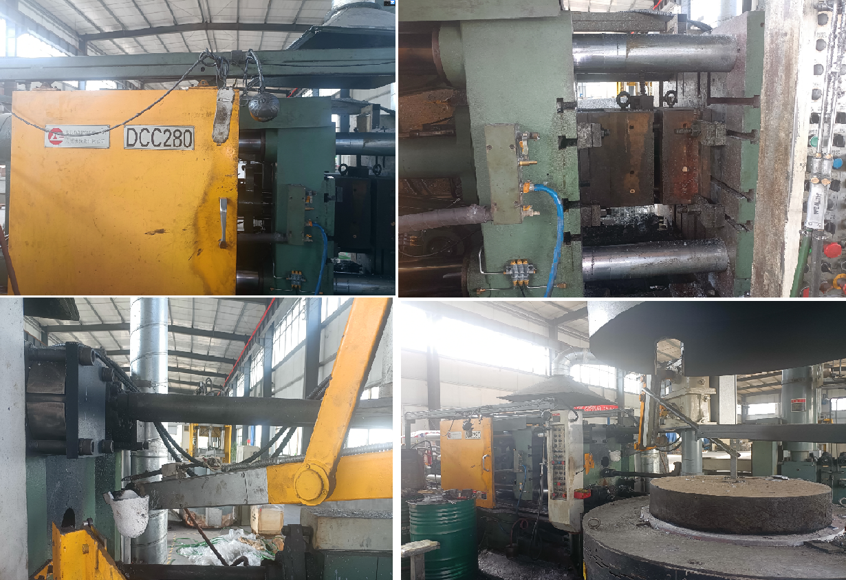
Die Casting Weights
0.07 in to 1,998 lbs. (0.03 to 908 kg) each casting.
Die Casting Size
Max. size 40 in x 79 in (1,000 mm x 2,000 mm) each casting.
Wall Thickness Range
Typical 0.03 in to 0.06 in (0.8 mm to 1.5 mm)
Annual Production
1,000 metric tons of cast products per Year.
Typical Materials
ASTM A380; ASTM A383 (ADC12, ADC 10), Alloys 102 and 104
Other materials include non-ferrous materials such as Bronze, Aluminum, etc.
Typical Investment Cast Products
High Speed Rail Parts, High Volume Industrial Parts, Valve and Pump Components, and many other parts.