Investment Casting Foundries
KEFA’s investment casting foundry is an industrial facility that specializes in the production of metal components using the investment casting process, also known as lost wax casting. This process allows for the creation of complex and intricate parts with high dimensional accuracy and surface finish.
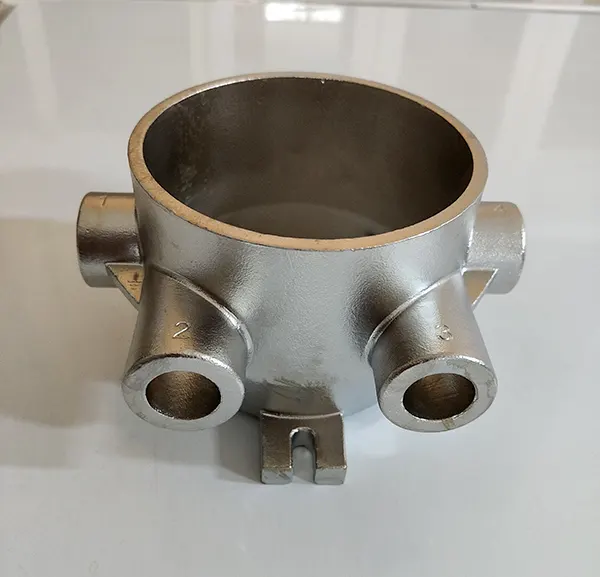
Below is a summary of the investment casting process in a foundry
A pattern, typically made of wax or a similar material, is created based on the desired shape of the final component. The pattern is an exact replica of the part and includes allowances for shrinkage and machining.
The pattern is then coated with a ceramic material through a series of dipping, stuccoing, and drying steps. This creates a ceramic shell around the pattern, forming the mold. The mold is built up layer by layer to achieve the desired thickness.
The ceramic shell mold is heated, causing the wax to melt and drain out. This step is known as dewaxing or wax elimination. It leaves behind a hollow cavity in the shape of the pattern within the ceramic shell.
The ceramic shell mold is preheated to remove any remaining moisture and increase its strength, making it ready for casting.
The molten metal cools and solidifies within the ceramic shell mold, forming the desired component.The cooling time depends on the size and complexity of the casting
The molten metal cools and solidifies within the ceramic shell mold, forming the desired component. The cooling time depends on the size and complexity of the casting.
Once the metal has solidified, the ceramic shell is removed by various methods such as mechanicalknocking, water blasting, or chemical dissolution. This reveals the solid metal casting
The casting may require additional operations such as cutting off excess material, grinding, machining,and surface treatments to achieve the desired final shape, dimensions, and surface finish
The finished casting undergoes inspection and quality control measures to ensure it meets the requiredspecifications and standards. Non-destructive testing, dimensional checks, and material analysis may beperformed
Depending on the desired properties of the metal, heat treatment processes such as annealing,quenching, and tempering may be applied to improve its strength, hardness, and toughness.
The finished castings are stored in designated areas and prepared for shipping to customers. Packaging, documentation, and logistics management are important aspects of this stage
complex and highly specialized facilities
Investment casting foundries require skilled technicians, metallurgists, and engineers to ensure precise pattern production, accurate metal pouring, and quality control. Advanced techniques and equipment such as autoclaves, furnaces, and wax injection machines may be used in the process.
Overall, an investment casting foundry plays a crucial role in producing intricate and high-quality metal components for various industries such as aerospace, automotive, medical, and industrial equipment manufacturing. The investment casting process offers the flexibility to create complex shapes and achieve tight tolerances, making it suitable for applications where precision and intricacy are required.
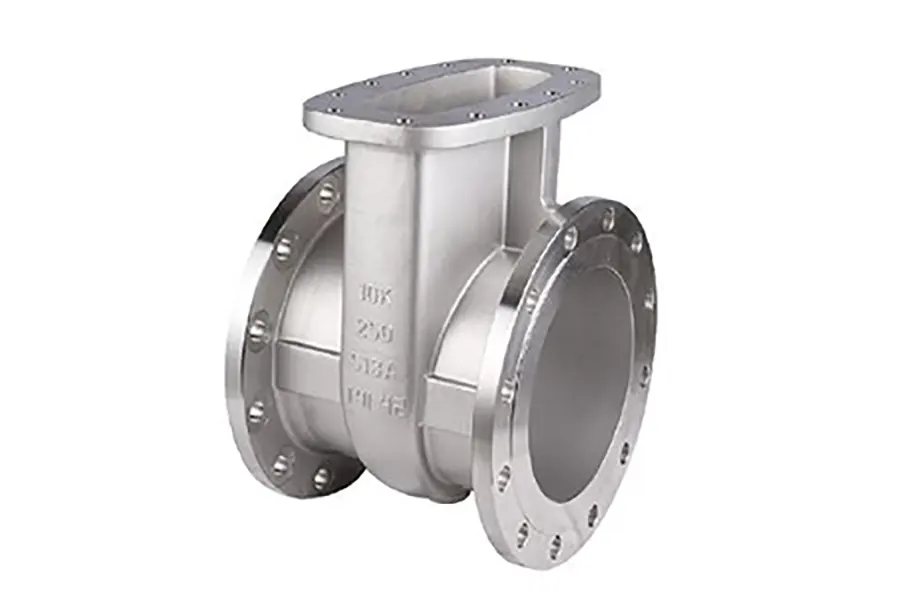
Casting Weights
From 0.022 to 770 lbs. (0.01 to 350 kg) each casting.
Annual Production
1,000 metric tons of cast products per Year.
Typical Materials
Stainless Steel: ASTM A351 Grade CF8/M/C;
Duplex Stainless Steel: CF3/M;ASTM A693 Grade 630; A890 Grade A1
Other materials include non-ferrous materials such as Bronze, Aluminum, etc.
Typical Investment Cast Products:
Valve Parts, Pump Parts, Automotive Components,Industrial Components,Hardware Components,Aerospace Parts, Medical InstrumentParts,Instrument Parts,Accessoriesand many other parts.
Industries Served
Industrial Equipment (Valves, Pumps, etc.),Automotive, Aerospace, Medical, Hardware, Instrumentation,and many other industries