Forged Steel Plant
In KEFA’s steel forging plants steel is shaped and formed into various components through the process of forging. The plants typically consist of several interconnected areas and machinery designed to heat, mold, and shape steel using compressive forces. The process of steel forging involves heating the steel to a specific temperature, known as the forging temperature, in a furnace. Once the steel reaches the desired temperature, it is transferred to a forging press or hammer. The press or hammer exerts immense pressure on the heated steel, deforming it and shaping it into the desired form. This process enhances the strength and durability of the steel by aligning its grain structure.
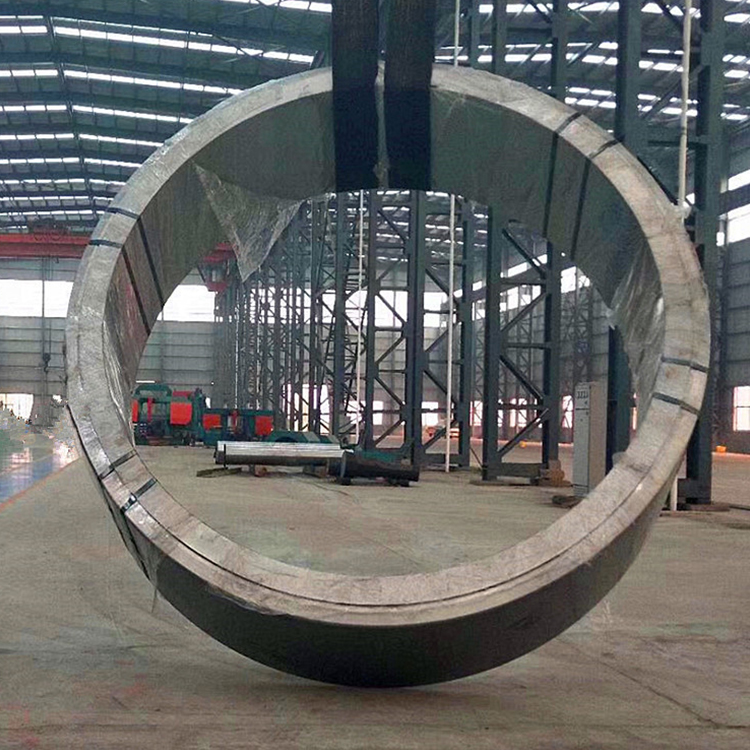
A steel forging plant generally comprises the following key components
This is where the steel is heated to the required forging temperature. The furnaces can use various heating methods such as induction, gas, or electric heating.
These heavy-duty machines exert tremendous force to deform the heated steel. Hydraulic or mechanical presses and power hammers are commonly used in steel forging plants. A 5,000-ton forging press, 3-ton and 5-ton forging hammers are used.
Dies are specialized tools used to shape steel. In this area, the dies are prepared and maintained. They are often made of high-strength materials to withstand the pressures and temperature involved in the forging process.
These machines assist in moving the heated steel to and from the furnace and positioning it under the forging press or hammer. They ensure safe and efficient handling of the material.
Quality control measures are implemented at various stages of the forging process. Non-destructive testing, dimensional checks, and other quality checks are performed to ensure the final products meet the required specifications and standards.
After the forging process, the steel components may undergo additional operations such as heat treatment, machining, surface finishing, and inspections to further enhance their properties and meet customer requirements. This includes a 30 foot (10 meter) annealing furnace.
After forging machining capabilities includes vertical and horizontal. CNC lathes, CNC boring and milling machines and hobbing machines.
Finished forged steel components are stored in designated areas and prepared for shipping to customers. Packaging, documentation, and logistics management are important aspects of this stage.
complex and highly specialized facilities
In KEFA’s complex and highly specialized facilities raw steel is transformed into strong, durable, and precisely shaped components which are used in various industries such as automotive, aerospace, construction, manufacturing, etc. These plants employ skilled trained technicians and engineers to operate and maintain plant equipment and processes, ensuring efficient production and adherence to quality standards.
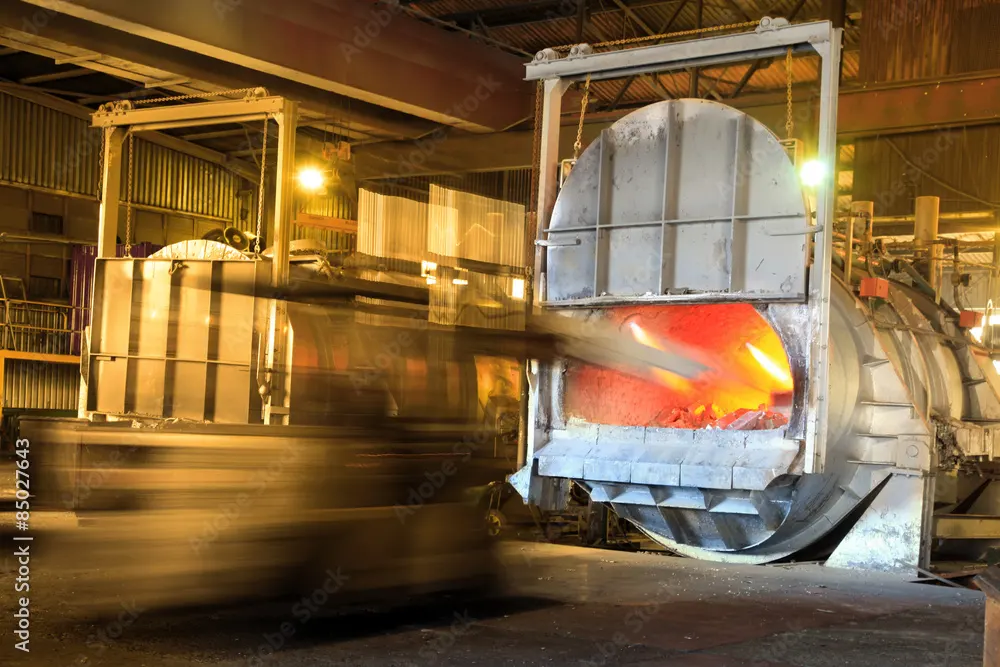
Annual Production
The annual forging capacity is 12,000 metric tons.
Typical Materials
Carbon Steel, Low Alloy Steel, Medium Alloy Steel, and High Alloy Steel
Typical Forged Products
Wheels, shafts, barrel forgings, ring forgings, pulleys, gears, hollow forgings, tubular forgings, plates, disks, valve bodies, forged pipes, pressure vessels and many other forged products.
Industries Served
Lifting Equipment, Electric Machinery, Rail Transit, Marine Products, Shipp Building, Petrochemical Industry, Electric Power Industry, Mining Machinery, Construction Equipment, Pressure Vessels, and many other industries.