KEFA Butterfly Valves are mechanical devices used to regulate the flow of liquids or gases in a pipe or tubing system. They consist of a circular disc or “butterfly” that is mounted on a rod within the valve body. The disc can be rotated by a handle or actuator to control the flow.
The disc of a butterfly valve is positioned perpendicular to the flow when closed, blocking the passage of fluid or gas. When the valve is opened, the disc is rotated parallel to the flow, allowing the medium to pass through with minimal obstruction. The degree of opening can be adjusted to regulate the flow rate.
Butterfly valves offer several advantages. They have a compact design, making them lightweight and easy to install. They provide quick and efficient on/off operation, allowing for rapid flow control. Butterfly valves also have a low pressure drop across the valve, resulting in minimal energy loss. They are available in various sizes, ranging from small to very large diameters.
One of the key benefits of butterfly valves is their cost-effectiveness. They are generally more affordable than other types of valves and require less maintenance. However, they may not be suitable for applications that require precise flow control or where high-pressure or high-temperature conditions are present.
Butterfly valves find applications in various industries, including water and wastewater treatment, HVAC systems, chemical processing, food and beverage, and pharmaceuticals. They are commonly used in systems where large flow volumes and moderate pressure conditions are encountered.
In summary, butterfly valves are versatile and cost-effective devices for regulating fluid or gas flow. Their simple design, quick operation, and low maintenance requirements make them suitable for a wide range of industrial and commercial applications.
- Double Offset Butterfly Valve
A KEFA Double Offset Butterfly Valve is a type of valve designed for regulating and isolating the flow of fluids in pipelines. It features a disc or plate that is positioned off-center from the valve’s shaft and seat. This offset design allows for a tight seal and improved performance.
The “double offset” refers to two offsets incorporated into the valve’s design. The first offset is the eccentricity between the shaft and the centerline of the valve, while the second offset is the offset between the disc’s centerline and the seat.
When the valve is closed, the disc is pressed against the seat, creating a seal and preventing leakage. As the valve opens, the double offset design reduces friction between the disc and the seat, allowing for smooth operation and precise flow control.
Double offset butterfly valves are widely used in various industries, including oil and gas, water treatment, chemical, and HVAC systems. They are suitable for medium to high-pressure applications and can handle a wide range of fluids.
A double offset butterfly valve provides reliable sealing, precise flow control, and durability. Its offset design minimizes friction and wear, making it a popular choice for industrial applications where efficient and accurate fluid regulation is required.
- Triple Offset Butterfly Valve
A KEFA Triple Offset Butterfly Valve is a high-performance valve designed for precise flow control and reliable sealing. It combines the features of a butterfly valve with three offsets or deviations from the centerline. The triple offset design allows the valve disc to make contact with the seat in a specific manner, ensuring a tight and bubble-tight seal. This design also reduces friction during operation, resulting in increased durability and extended service life. Triple offset butterfly valves are commonly used in industries that require efficient flow control, such as oil and gas, chemical, power generation, and water treatment. They offer improved sealing capabilities, reduced torque requirements, and are suitable for high-pressure, high-temperature, corrosive, or abrasive fluid applications.
Typical Size Ranges: From 3 in through 78 in (DN 50 to DN 2000)
Typical Pressure Classes: ANSI 125, 150, 300 and 400 (PN 16, 20, 50 and 64)
Typical Temperature Ranges: -40 F to 1022 F (-40 C to 550 C)
Typical Materials: Body: 304 Stainless Steel
Seat: 420 Stainless Steel & Graphite
Disc: 304 Stainless Steel
Stem: 304 or 420 Stainless Steel
For applications with specifications deviating from the once listed above, please contact factory for a quote.
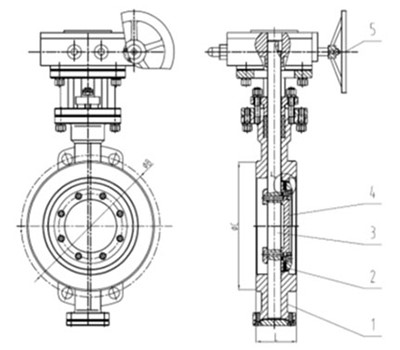
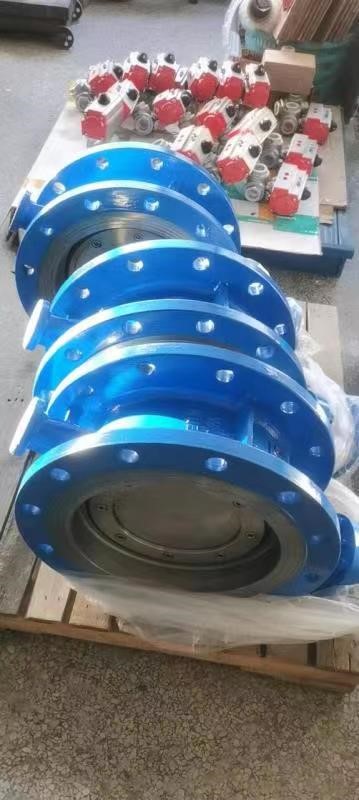