Sand Cast Foundries
KEFA’s steel sand-casting foundries are industrial facilities that specialize in producing steel castings using the sand-casting process. Sand casting is a simple and widely used method for manufacturing complex metal parts by pouring molten metal into a sand mold.
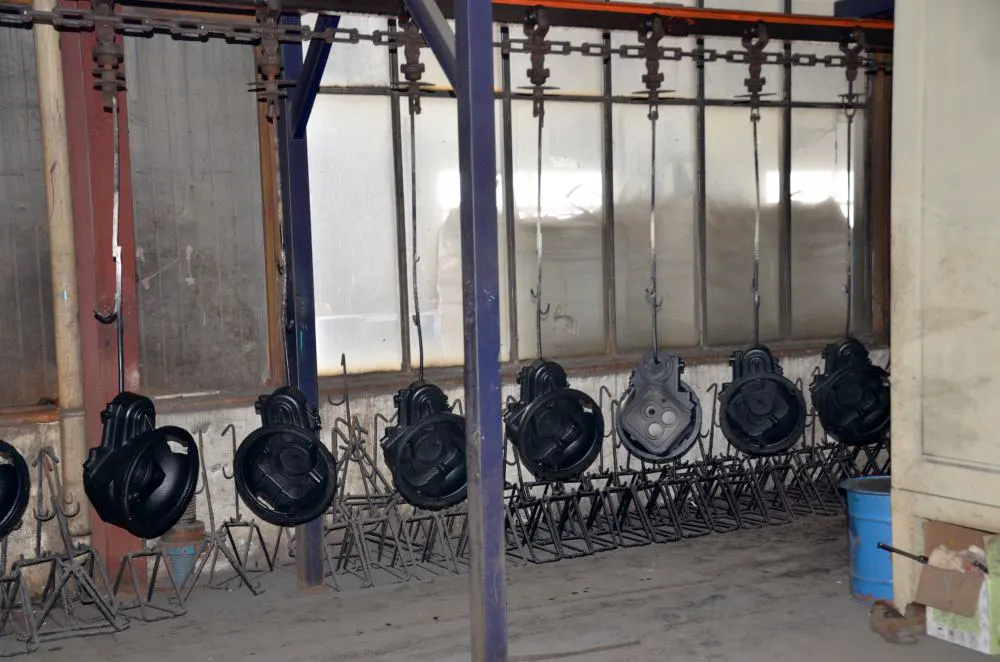
In a steel sand casting foundry, the process typically involves the following steps:
A pattern, typically made of wood, is created based on the desired shape of the final casting. The pattern is a replica of the part and includes allowances for shrinkage and machining.
Sand molds are made by packing a mixture of sand and a bonding agent, such as clay or resin, around the pattern. The mold is usually composed of two halves, known as the cope and drag. Cores, which are sand structures used to create internal cavities, are also made if required.
Steel is melted in a furnace, typically an electric arc furnace or an induction furnace, to reach the required casting poring temperature. Once reached, the steel is poured into the prepared sand mold, filling the cavity.
The molten steel cools and solidifies within the mold, taking the shape of the pattern. The cooling time depends on the size and thickness of the casting.
After the steel has solidified, the sand mold is broken apart to remove the casting. This is typically done by vibrating or mechanically breaking the mold. The casting is then separated from the sand and cleaned.
The casting may require additional operations such as cutting off excess material, grinding, machining, and surface treatments to achieve the desired final shape, dimensions, and surface finish.
The finished casting undergoes inspection and quality control measures to ensure it meets the required specifications and standards. Non-destructive testing, dimensional checks, and material analysis may be performed.
Depending on the desired properties of the steel, heat treatment processes such as annealing, quenching, and tempering may be applied to improve its strength, hardness, and toughness.
The finished castings are stored in designated areas and prepared for shipping to customers. Packaging, documentation, and logistics management are important aspects of this stage.
complex and highly specialized facilities
A steel sand casting foundry requires skilled technicians and metallurgists to ensure proper mold preparation, accurate pouring, and quality control. The foundry also has auxiliary equipment such as furnaces, sand preparation systems, and molding machines to support the casting process.
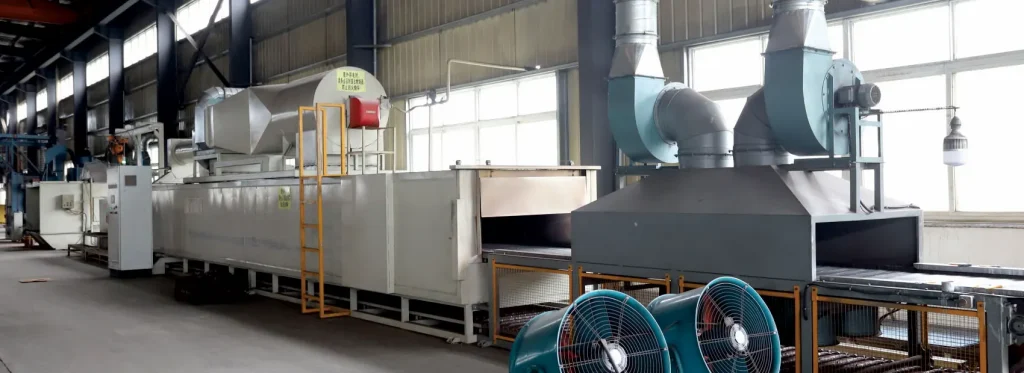
Casting Weights
1.1 to 11,000 lbs. (0.5 to 5,000 kg) each casting.
Annual Production
2,000 metric tons of cast products per Year.
Typical Materials
Gray Iron: ASTM A48 Class 20, 25, 30, 40, 45, 50,55 and 60
Ductile Iron: ASTM A536 Grade 60-40-18, 56-45-12; 80-65-06; 100-70-03
Steel: ASTM A216 WCA/WCB/WCC; ASTM A352 LCB/LCC
Cast Steel: AISI1020, 1030, 1040, 4130 ,432H, 4330, 4340, 8620 and 8630
Stainless Steel: ASTM A351 Grade CF8/M/C; CF3/M
Duplex Stainless Steel: ASTM A693 Grade 630; A890 Grade A1
Other materials include non-ferrous materials such as Bronze, Aluminum, etc.
Typical Forged Products
Valve Parts, Pump Parts, Industrial Components, Mining Parts, Agricultural Parts and many other parts.
Industries Served
Industrial Equipment (Valves, Pumps, etc.), Mining, Agriculture, and many other industries.